Think of the Atlanta airport terminal and the large maze that is the line that twists and turns, back and forth, to get travelers to security checkpoints.
At Volkswagen's Chattanooga plant, the company has set up a similar operation as employees enter the factory each day, but with social distancing. Workers make their way through the maze where their temperatures are taken by touch-less thermometers and they're questioned if they're sick or contacted anyone who is.
It's one of the steps VW officials said they've taken to fight COVID-19 and keep workers healthy as they return from a nearly two-month-long shut down. Manufacturers in the Chattanooga area that closed during the coronavirus lockdown are reopening and taking a variety of measures to safely restart production.
Tom du Plessis, VW Chattanooga's chief executive, said the mood of employees concerning the 90 or so new safety measures the automaker has put into place is "predominately positive."
"I've found no one saying they don't want to be here," he said. "We call it the 'now normal."'
VW said the plant has staggered start times of its shifts so employees don't arrive at once at the factory's large conference center. Workers are all given a face mask each day if they don't already have one. They pass through the airport-like maze before going to their various work stations.
Marsha Wood, the plant's assistant manager for health and wellness, said VW has weekly global meetings aimed at keeping employees safe. The company has learned what worked in Europe and China, where the automaker has a number of plants.
"They got it first," she said about those countries and the coronavirus.
The plant is going through four phases of restarting assembly, du Plessis said. With all the safety steps, VW is taking it slow and starting at just 50% production, he said. He expects to be up to full production next month if all goes well.
While VW had been in a hiring mode with plans to bring on about 600 new employees to the 3,800 already on board at the plant, du Plessis said the automaker will do a reassessment in the wake of COVID-19.
"We've not made a decision," he said, adding that construction is ongoing on a plant expansion to build electric vehicles.
Slow restart at La-Z-Boy
In Dayton, Tennessee, furniture-maker La-Z-Boy shut its large, 1,400-person factory in March.
The company restarted its facility on April 27 with about 540 employees and its headcount was some 715 last week, said Kathy Liebmann, La-Z-Boy's director of investor relations and corporate communications.
"We will operate the business as customer demand dictates and are hopeful that as more retailers are permitted to reopen, we will be able to increase production accordingly and bring more employees back to work," she said. Liebmann said production is at about 47% of plant capacity.
Concerning employee safety, she said La-Z-Boy has built upon practices that were already in place in its facilities. The company is following guidelines from the Centers for Disease Control and the World Health Organization, Liebmann said.
While La-Z-Boy plants were closed, the company engaged in a deep cleaning of the facilities, including electrostatic sanitation across all plant work stations, she said. Filters and air-handling systems were cleaned and sanitized.
"Deep cleaning and enhanced sanitizing continues every day," Liebmann said.
Also, the plant offers a Daily Health Surveillance program that includes temperature checks for employees as well as a symptom and exposure survey.
Much of the furniture production at the plant revolves around work cells, or clusters of people. Liebmann said the cells and those areas have been staged to comply with social distancing requirements.
La-Z-Boy also has staggered start and break times to comply with social distancing.
"We also ensure employees have access to an abundance of hand sanitizer, EPA- and CDC- approved disinfectant spray and fresh face masks so we can provide a safe and healthy environment for everyone," Liebmann said.
Nokian Tyres restarts
Not far away in Dayton at one of the newest factories in Southeast Tennessee, tire producer Nokian Tyres returned from a shut down with its first group of employees on April 27, said company spokesman Wes Boling. A full reopening was carried out May 4, he said.
With just more than 100 workers, the plant is at about where it was before the shut down and at a fourth of its eventual employment, he said.
Nokian is allowing only business-critical visitors onto the factory site, though construction is ongoing on the company's administration building, the spokesman said.
Boling said the factory has eliminated factory-wide, in-person meetings and is communicating virtually instead, as needed. Nokian is taking temperature screenings of workers each day, providing masks to all employees and enforcing strict social distancing, along with rotating entry times and lunch breaks, he said.
"We've increased the frequency of cleaning," Boling said.
At VW, as employees walk through the tunnel connecting the conference center with the production lines, video screens remind workers about the new COVID-19 safety measures.
Cleaning and separation
Even before bringing workers back to the plant, du Plessis said VW and other automakers shared information about safety practices. VW also communicated with its workforce while they were still at home, and it has passed on safety steps to companies operating at the plant's adjacent supplier park, he said.
Dean Parker, the plant's head of manufacturing, said multiple cleanings are taking place at work stations and on the variety of tools used by employees.
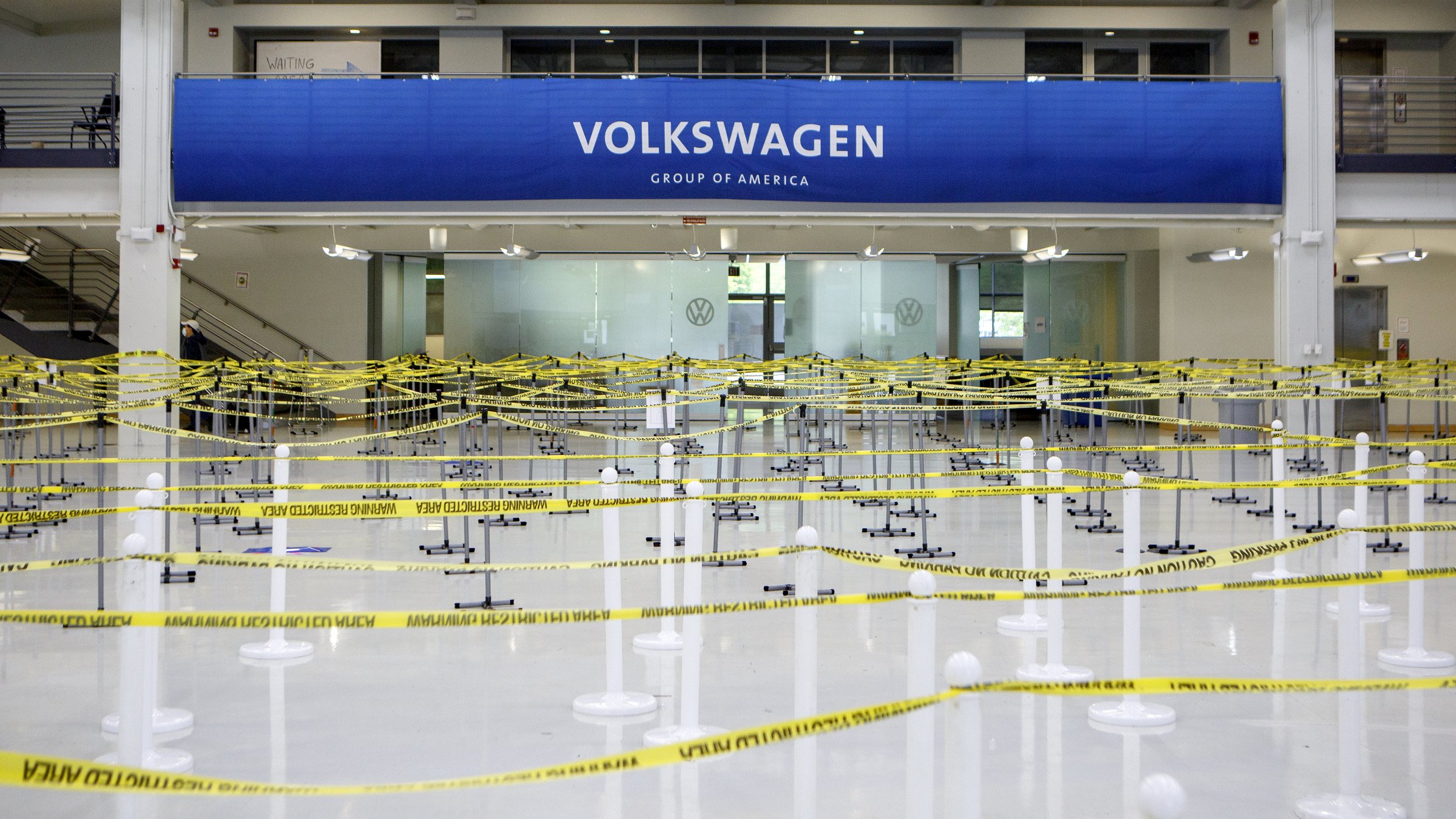
"We're taking our time with the team," he said. "We take time to clean tools. It's frequency of cleaning."
Parker, who heads a 25-person task force at the plant that meets daily, pointed out that line employees who typically work close to one another are now separated by screens. Another measure was creation of a shower curtain-type device that magnetically attaches under a vehicle's engine hood to help social distance two workers, he said.
Dr. Mark Anderson, an infectious disease specialist at CHI Memorial in Chattanooga, toured the plant recently and reviewed VW's new safety processes.
Anderson said he was "really impressed" with the preparations VW made, citing its thoroughness. Putting people in masks and keeping them on them all day is important, he said.
"It has been a game-changer at Memorial," Anderson said.
Also, putting in hand sanitizing stations in the plant is key, he said.
"I do feel it's safe," Anderson said about the plant.
Amanda Plecas, VW Chattanooga's head of communications, said the company has put partitions on the top of tables at places where workers take breaks and in the cafeteria, which now looks like a large room where people vote during an election.
Worker pay card kiosks have been shifted away of one another to encourage social distancing, more microwave ovens have been installed and there's a lot of individually wrapped grab and go meals offered to employees, she said.
Contact Mike Pare at mpare@timesfreepress.com. Follow him on Twitter @MikePareTFP.